Case Study: HP500 Tertiary Crushing — TIM Liners Deliver 55% Longer Life and Higher Throughput
In April–May 2025, TIM conducted a performance test on our proprietary IMTUFF® TIM liners installed on a Metso HP500 Short Head crusher. The operation involved the tertiary crushing of surface volcanic iron ore with copper content, averaging a grade of 17.5%, a Proctor scale hardness of 10–12, and a bulk density of 1.8 t/m³. The results clearly demonstrated the value of TIM’s liner design and optimisation methodology.
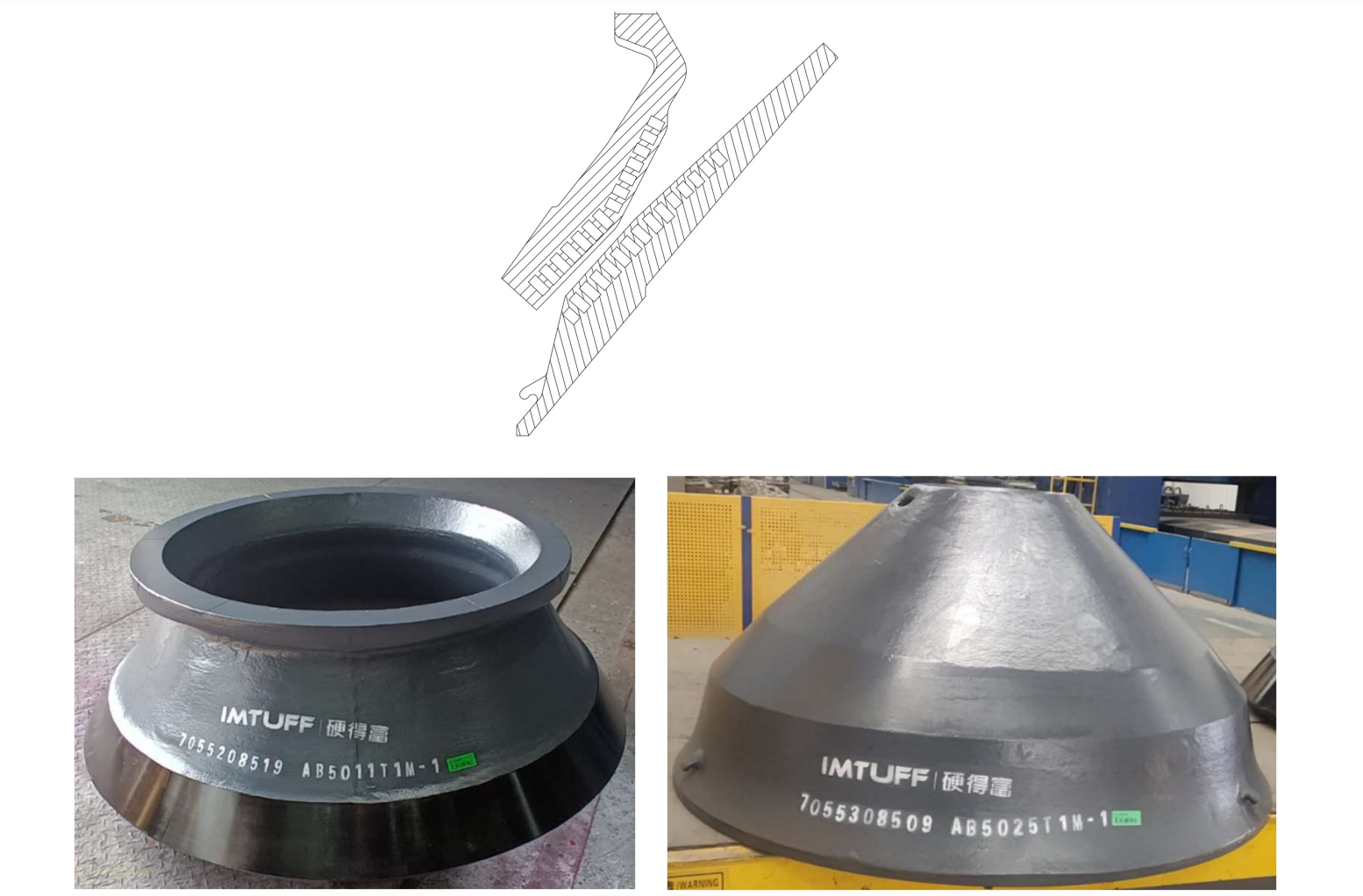
Performance Highlights
Crushing setup: Tertiary crushing with choke feeding
Feed size (F80): 50 mm
Discharge size (P80): 12 mm
Liner life: 40 days
Total throughput achieved: 350,000 tons
Previous benchmark: 225,000 tons using standard 18% manganese liners
Compared to standard manganese liners, the TIM solution delivered a 55% increase in throughput, while maintaining excellent wear balance across mantle and bowl liners.
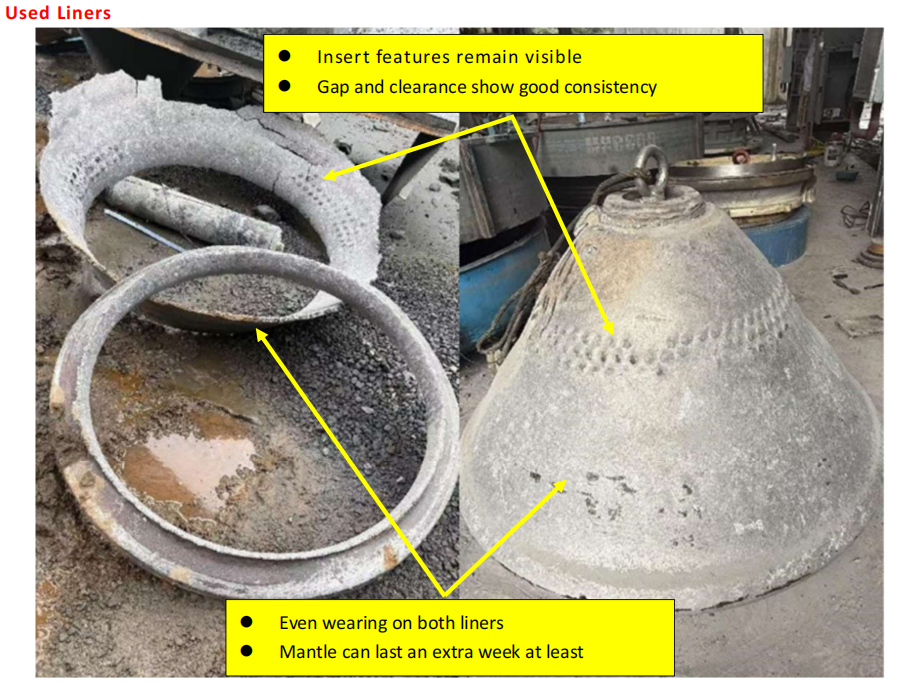
Key Observations
The bowl liner was worn out and cracked, prompting scheduled replacement.
The mantle was still in good condition and could have remained in service for an additional week.
Both liners exhibited even wear patterns, and insert features remained clearly visible, especially in the secondary crushing zone.
Gap and clearance measurements showed high consistency, reflecting stable operating performance.
TIM Optimization and Future Outlook
Based on performance insights, TIM implemented the following optimizations:
Clearance Adjustment: 10 mm at the parallel zone, 15 mm at the secondary zone
Bowl Liner Reinforcement: To achieve balanced wear with the mantle
Projected Throughput: 400,000–450,000 tons for future liner sets under similar conditions
With these optimisations, we expect a further 15–30% gain in service life, supporting our clients’ goals of increasing plant uptime and reducing liner change frequency.
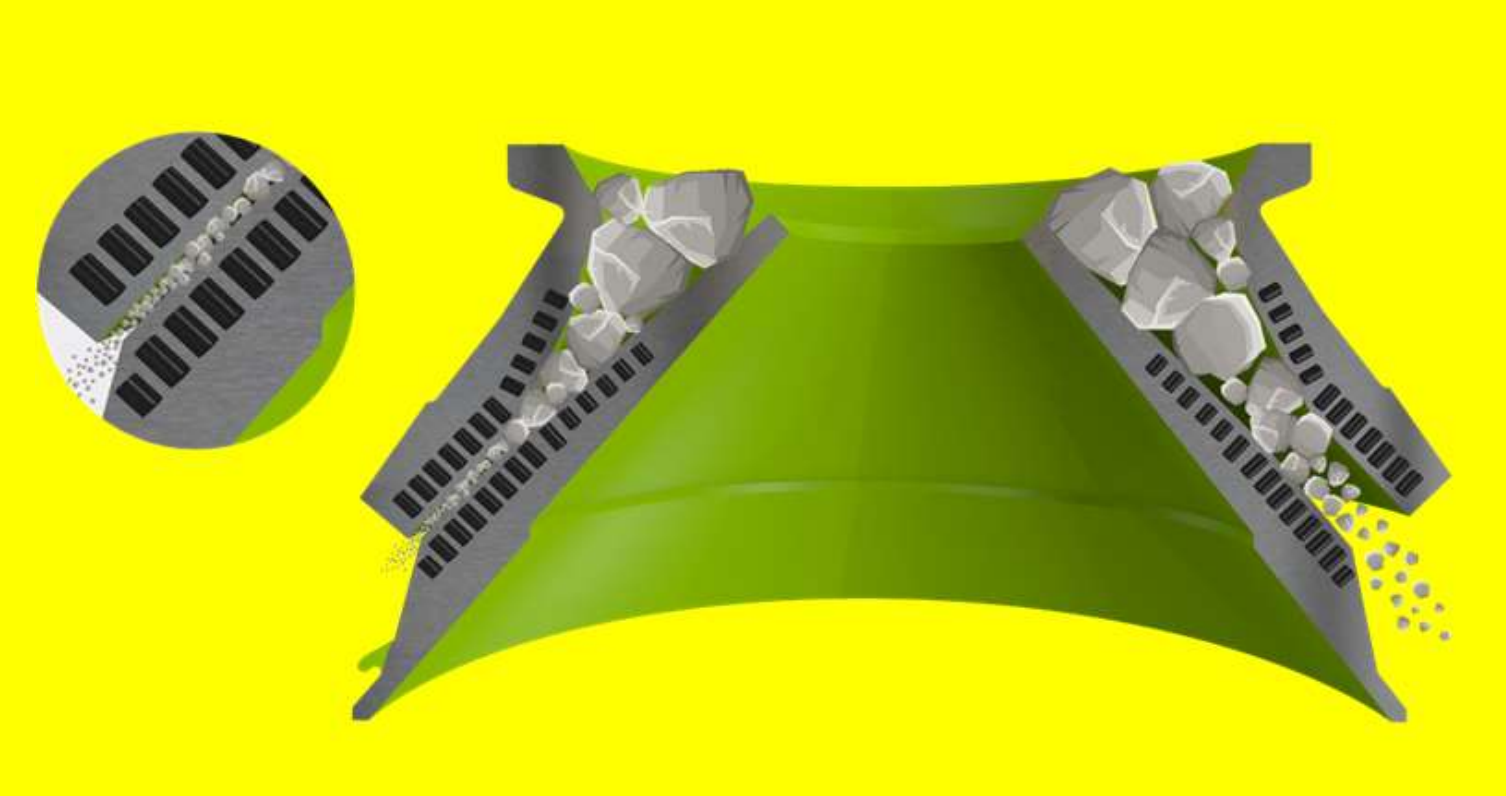
About IMTUFF® TIM Liners
Launched in 2021, our TIM liners represent a new standard in high-performance crushing wear parts:
Machined and pre-hardened to the same standards as conventional manganese liners
Feature engineered insert technology to absorb and redistribute crushing stress
Enable more effective work-hardening in high-impact zones
Proven success across primary, secondary, and tertiary crushing applications
Conclusion
This case confirms TIM’s ability to deliver significantly higher liner performance in challenging crushing environments. For operators seeking longer wear life, more consistent crushing performance, and higher throughput per liner set, TIM liners offer a measurable return on investment.
To learn more about our crushing liner technologies or to request a custom evaluation, please contact our team.
Related articles